Decarbonising white cement | International Cement Review
While the decarbonisation of grey cement production has gathered considerable pace, reducing the carbon footprint of white cement production brings its own challenges. Cementir highlights the development path of its lower-carbon white cement, D-Carb®.
As the world’s leading producer of white cement with over 3Mta of capacity, and accounting for a ~25 per cent share of global white cement trade, Cementir Group – through its global brand Aalborg White® – has played a pivotal role in the construction of many iconic structures: from the Kennedy Centre for the Performing Arts in Washington, USA, to the Naturalis Biodiversity Centre in Leiden, The Netherlands, and from Azabudai Hills in Tokyo, Japan, to the Mei Xi Hu International Culture and Art Centre in Changsha, China.
The main distinctive features of white cement are its light colour and high performance, achieved through the meticulous selection of highly pure and carefully-selected raw materials, complex production processes and a rigorous quality control process.
However, when compared with grey cement manufacture, transitioning towards more sustainable white cement production is significantly more challenging, due to major differences in the production process as well as the need to guarantee colorimetric performances. Common actions to reduce the carbon footprint of grey cement production, such as the use of alternative fuels and supplementary cementitious materials (SCMs), are not suitable for white cement production. The use of alternative fuels in white cement production is limited due to the negative impact on colorimetric performances. However, at its white cement plant in Aalborg, Denmark, Cementir Group has partially mitigated its environmental impact through the use of waste heat recovery (WHR) technology. The plant is equipped to recover excess heat from cement production and provides district heating to ~30,000 local households. In 2022 alone, the Aalborg plant delivered ~1.3mGJ of energy, avoiding the emission of an estimated 150,000t of CO2 emitted by a local coal-fired power station.
In addition, SCMs used in grey cement production to reduce the clinker- to-cement ratio present challenges when used in white cement production. Nearly all of these materials negatively impact the whiteness of white cement, its distinctive value proposition when compared with grey cement. Therefore, the selection, availability and quality consistency of materials are important when reducing the carbon footprint of white cement production.
Paving the way for white cement decarbonisation
Despite the difficulties presented, Cementir has embraced the challenge of lowering the carbon footprint of white cement, taking into account colour and performance requirements. To achieve the decarbonisation of white cement production, the group leveraged its long-term expertise in research and development as well as white cement production to carry out a comprehensive investigation, starting with customer requirements and going upstream to cover the entire value chain, including clinker and cement composition, production and raw materials selection.
To provide a solution to customer requirements in terms of end-applications, the group has established technical collaborations with leading companies in the admixtures sector as well as in-depth meetings with loyal customers to inform product design.
Moreover, to accelerate the time-to- market that addresses the need of more sustainable solutions, fast-prototyping techniques were deployed, involving extensive experimentation at laboratory- and full-scale trial levels.
As a result of this research and development programme, Cementir is launching its D-Carb® range, representing a continuous and consistent decarbonisation effort for the Aalborg White® range.
D-Carb will be firstly rolled out in Europe, followed by other regions. CEM II/A-LL 52.5R will be the first product of the company’s D-Carb family. Its initial production will take place at the Aalborg Portland plant, where it is set to be launched during April 2024. It will be available both in bulk and bags, strengthening its product range in Europe.
Benefits of lower-carbon white cement
D-Carb has a lower-carbon footprint with global warming potential (GWP/ A1-A3) at 828kg of CO2/t (documented with Environmental Product Declaration), representing a 15 per cent reduction of CO2 emissions when compared with Aalborg White CEM I 52.5R. D-Carb is the first in the market to match a lower-carbon footprint with outstanding performances at early ages.
D-Carb also inherits the extra properties given by the Aalborg White® clinker used, benefiting from particularly low C3A, extremely low alkali and low chloride content.
Moreover, with its white colour as a key feature, exploring suitable raw materials has been a cornerstone in the full product assessment. This has led to the accurate choice of a pure and very light limestone from a stable source, resulting in an improved and stable whiteness that is appreciated in several applications where whiteness purity is a must.
Furthermore, leveraging the limestone fineness as well as the overall particle size distribution, D-Carb allows an enhanced and consistent rheology considered as a seal of quality in wet-cast applications that mainly use self-compacting concrete. These superior rheological properties enable customers to achieve a finishing resembling a marble surface.
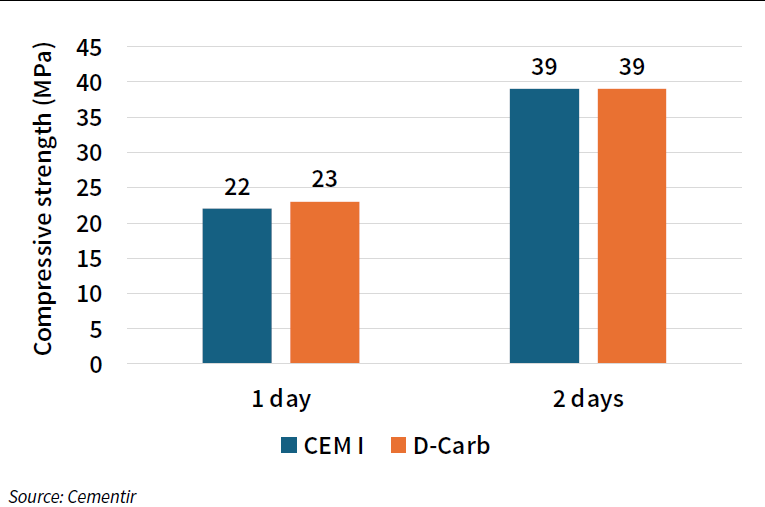
Thanks to in-house extended expertise in white cement production technology, the synergy between well-known Aalborg White clinker and limestone has been optimised by choosing a fit-for-purpose grinding aid to achieve an outstanding performance at early ages comparable to Aalborg White CEM I 52.5R, as shown in Figure 1. This is a great achievement given that limestone is not considered as a reactive addition (SCM).
Acknowledging the critical importance of the synergy between cement and admixtures, no incompatibility has been experienced during the extensive experimental phase, which covered all types of applications. In this study all leading admixtures on the market were tested, while also establishing collaboration with the main producers to deep dive into the system cement/admixtures/other components of the mixes. During this extensive testing programme, further benefits were found in each application investigated:
• semi-dry cast concrete products
- carbon footprint - finishes and surfaces
- pre-stability and edge solidity
- density and strengths.
• tile adhesive
- carbon footprint
- consistency/ workability.
• brick laying mortar
- carbon footprint
- consistency/workability
- high early strength with balanced long-term strength.
• wet-cast concrete products
- carbon footprint
- SCC robustness with less segregation and bleeding
- less admixture.
White cement transition
Thanks to the overall performance achieved by D-Carb, through a specific testing programme, customers will be able to replace CEM I 52.5R in their construction projects, particularly in applications that demand an improved early age performance. To support this transition to lower-carbon white cement use, Cementir Group will leverage its technical experts to guide users in adopting D-Carb white cement in their projects.
As part of Cementir Group’s wider decarbonisation roadmap and to meet the growing global demand for low- carbon products, further assessments are underway to strengthen the D-Carb range with other more sustainable solutions.